What Is an ISO 6 Cleanroom Classification? Standards and Requirements
An ISO 6 cleanroom represents a specific level of air cleanliness within controlled environments that facilitates manufacturing processes requiring high levels of particulate control. Pharmaceutical cleanrooms and environments help prevent contamination that could compromise product quality or research integrity while maintaining precise temperature and humidity conditions for optimal manufacturing outcomes.
Let Precision Environments handle your cleanroom design and engineering
needs with proven results that exceed ISO standards
Facing contamination control challenges?
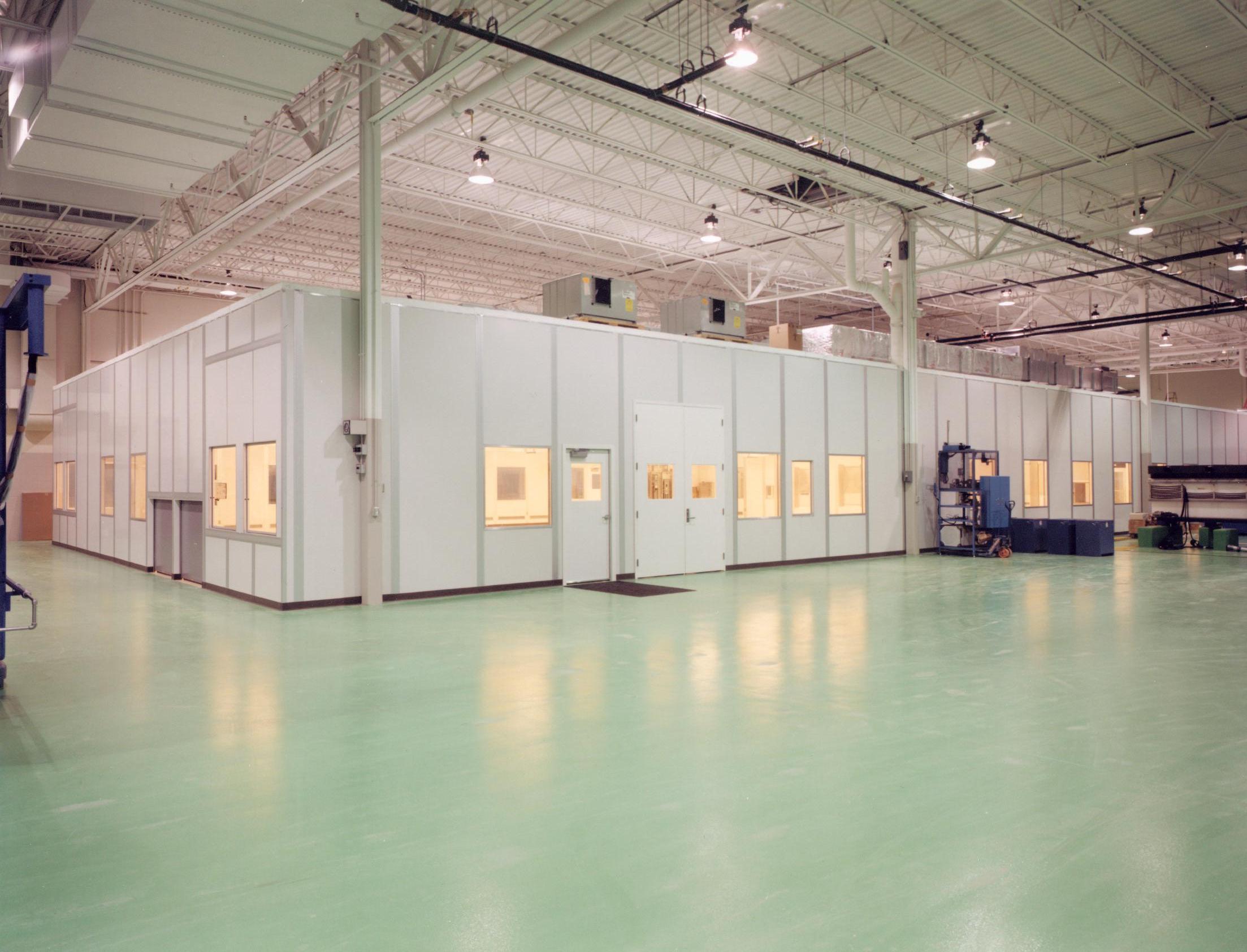
ISO Cleanroom Classifications Explained
The International Organization for Standardization (ISO) developed standards to provide consistent metrics for cleanroom environments worldwide. These standards establish clear parameters for particulate control and enable manufacturers to create appropriate environments for their specific production needs:
ISO 14644-1 Standards Framework
ISO 14644-1 defines cleanrooms by measuring airborne particulate concentration, establishing nine classifications (ISO 1 through ISO 9). Each level specifies maximum allowable concentrations of particles per cubic meter at specified particle sizes. This framework enables designers and manufacturers to select the appropriate classification based on process requirements and provides measurable criteria for certification and ongoing performance verification that cover cleanliness standards, temperature stability, and humidity control.
See our ISO 5 cleanroom designs for solving complex manufacturing challenges.
The Role of Cleanroom Classifications in Manufacturing
Cleanroom classifications directly impact manufacturing quality and consistency through these mechanisms:
- Controlled environments prevent contamination from particles, microbes, and other pollutants
- Precision manufacturing processes depend on appropriate classifications and environmental containment
- Classification levels ensure compliance with specific industry sector requirements, including temperature, humidity, and pressurization standards
- Proper classifications safeguard product performance and integrity throughout production
Upgrade your facility with cleanroom filtration and HVAC systems that deliver consistent classification performance.
Where ISO 6 Fits in the Classification Spectrum
ISO 6 occupies the middle range of industrial cleanrooms and classifications, providing a balance between stringent cleanliness requirements and operational practicality. With a maximum particle count of 35,200 particles per cubic meter (≥0.5μm), ISO 6 environments are significantly cleaner than standard industrial spaces but less restrictive than the ultra-pure environments required for semiconductor fabrication. This classification serves many advanced manufacturing applications that need substantial particulate control without the extreme requirements of higher classifications, while still maintaining effective containment and environmental stability.
Build a production-ready ISO 7 cleanroom tailored to your industry requirements.
Design Requirements for ISO 6 Cleanroom Implementation
Creating and maintaining an ISO 6 cleanroom requires specific design elements and operational systems. Cleanroom environments must incorporate particular features to maintain classification standards while supporting production workflow:
Particle Count Limits and Air Quality Parameters
ISO 6 cleanrooms must maintain particle counts below 35,200 particles per cubic meter for particles ≥0.5μm and 832 particles per cubic meter for particles ≥5.0μm. Achieving quality standards requires precise control of airflow, filtration, and room pressurization. Air cleanliness is continuously monitored to verify compliance with ISO 14644-1 standards, with regular particle testing confirming the environment meets classification requirements, alongside temperature and humidity monitoring.
HVAC and Filtration System Specifications
The HVAC system forms the backbone of any ISO 6 cleanroom design, incorporating several key components:
- HEPA filtration (99.97% efficient at 0.3μm) or ULPA filters for more stringent applications
- Air change rates typically ranging from 60 to 90 air changes per hour
- Unidirectional air flow patterns that sweep particles away from critical work areas
- Ceiling systems with filter coverage appropriate to classification level and process requirements
Personnel and Material Flow Planning
The movement of people and materials represents a significant contamination risk in cleanroom environments. Properly designed ISO 6 cleanrooms include gowning rooms with appropriate protocols for personnel entry and exit. Material transfer systems such as pass-through chambers with interlocking doors prevent direct air exchange with less controlled areas. The people working inside must follow strict procedures to minimize particle generation during operations.
Let Precision Environments handle your cleanroom design and engineering
needs with proven results that exceed ISO standards
Facing contamination control challenges?
Primary Applications for ISO 6 Cleanroom Environments
ISO 6 modular cleanrooms serve diverse industries requiring precision-controlled manufacturing environments:
Semiconductor Production Requirements
While the most advanced semiconductor processes require higher classifications, many semiconductor auxiliary operations and packaging processes utilize ISO 6 environments. Cleanrooms protect sensitive electronic components from particulate contamination that could cause shorts, open circuits, or other defects.
Medical Device Manufacturing
Medical device cleanrooms often utilize ISO 6 classification to maintain product sterility and quality:
- Equipment inside these environments is tailored for manufacturing processes while minimizing particulate generation
- ISO 6 environments support implantable and sterile medical device production applications with strict containment protocols
- Design accommodates specific workflow requirements for medical component assembly, including precise temperature and humidity control for material stability
- Monitoring systems verify that environmental conditions meet regulatory standards for cleanliness, pressurization, and climate control
Aerospace Component Fabrication
Aerospace manufacturing requires exceptional precision and reliability. ISO 6 cleanrooms provide appropriate environments for manufacturing critical components where contamination could compromise safety or performance. Controlled environments help maintain the exacting standards required for aerospace applications.
Maintaining ISO 6 Cleanroom Certification
Establishing an ISO 6 environment is only the beginning—maintaining classification requires ongoing attention to multiple factors:
Cleaning Protocols and Maintenance
Protocols and cleaning procedures using appropriate materials and techniques help maintain ISO 6 classification standards. Surfaces must be designed for easy cleaning with minimal particle generation. Regular maintenance schedules for all systems, particularly HVAC components, prevent performance degradation over time and ensure consistent cleanliness levels throughout the facility.
Environmental Monitoring Approaches
Continuous or periodic monitoring systems track multiple parameters in ISO 6 cleanrooms:
- Particle counts measured against ISO 14644-1 standards
- Pressurization differentials maintained between adjacent spaces
- Temperature and humidity levels monitored for process stability and containment effectiveness
- Data collection systems provide documentation for certification compliance and cleanliness verification
Personnel Training Requirements
Staff working in ISO 6 environments require intricate training on proper gowning procedures, movement restrictions, and contamination control practices. Continuous training updates and procedural reviews increase awareness and compliance with cleanroom protocols that preserve containment integrity and maintain cleanliness standards.
Let Precision Environments handle your cleanroom design and engineering
needs with proven results that exceed ISO standards
Facing contamination control challenges?
ISO 6 Cleanroom Solutions by Precision Environments
Since 1989, Precision Environments has designed and built controlled environments for diverse industries requiring stringent contamination control. With experience constructing over 1,000 environments across 15 countries, our engineering team delivers ISO-classified cleanrooms that meet exact specifications for particle control, temperature stability, humidity management, and advanced process requirements, including containment solutions and pressurization systems. Our turnkey approach covers planning through certification, with ongoing maintenance services to ensure continued performance. Contact our team to discuss your ISO 6 cleanroom requirements and discover how our expertise can support your manufacturing goals.
Frequently Asked Questions
How do you classify a clean room in CFU?
Clean rooms can be classified using Colony-Forming Units (CFU) measurements, which count viable microorganisms per cubic meter of air. This microbial classification system complements the particle count measurements defined in ISO standards, with ISO 6 environments typically maintaining levels below 100 CFU/m³ while ensuring proper temperature, humidity, and containment controls to prevent microbial growth.
Which cleanroom is the cleanest?
ISO 1 cleanrooms represent the cleanest classification in the ISO 14644-1 standard, permitting only 10 particles ≥0.1μm per cubic meter. These ultra-pure environments require extraordinarily sophisticated design, construction, and operational protocols to maintain such extreme cleanliness levels, primarily used in specialized semiconductor manufacturing processes that demand strict temperature control, humidity management, pressurization precision, and absolute containment.