What Is a Cleanroom in Pharma? Understanding Their Role in Drug Manufacturing
Pharmaceutical cleanrooms are specialized controlled environments designed to minimize contamination while manufacturing pharmaceutical products. Quality cleanroom environments maintain precise control over airborne particles, temperature, humidity, and pressure to protect product integrity and ensure patient safety. A properly designed and built pharmaceutical cleanroom provides the foundation for contamination prevention, much like a well-constructed roof protects a home from leaks.
Let Precision Environments handle your cleanroom design and engineering
needs with proven results that exceed ISO standards
Facing contamination control challenges?
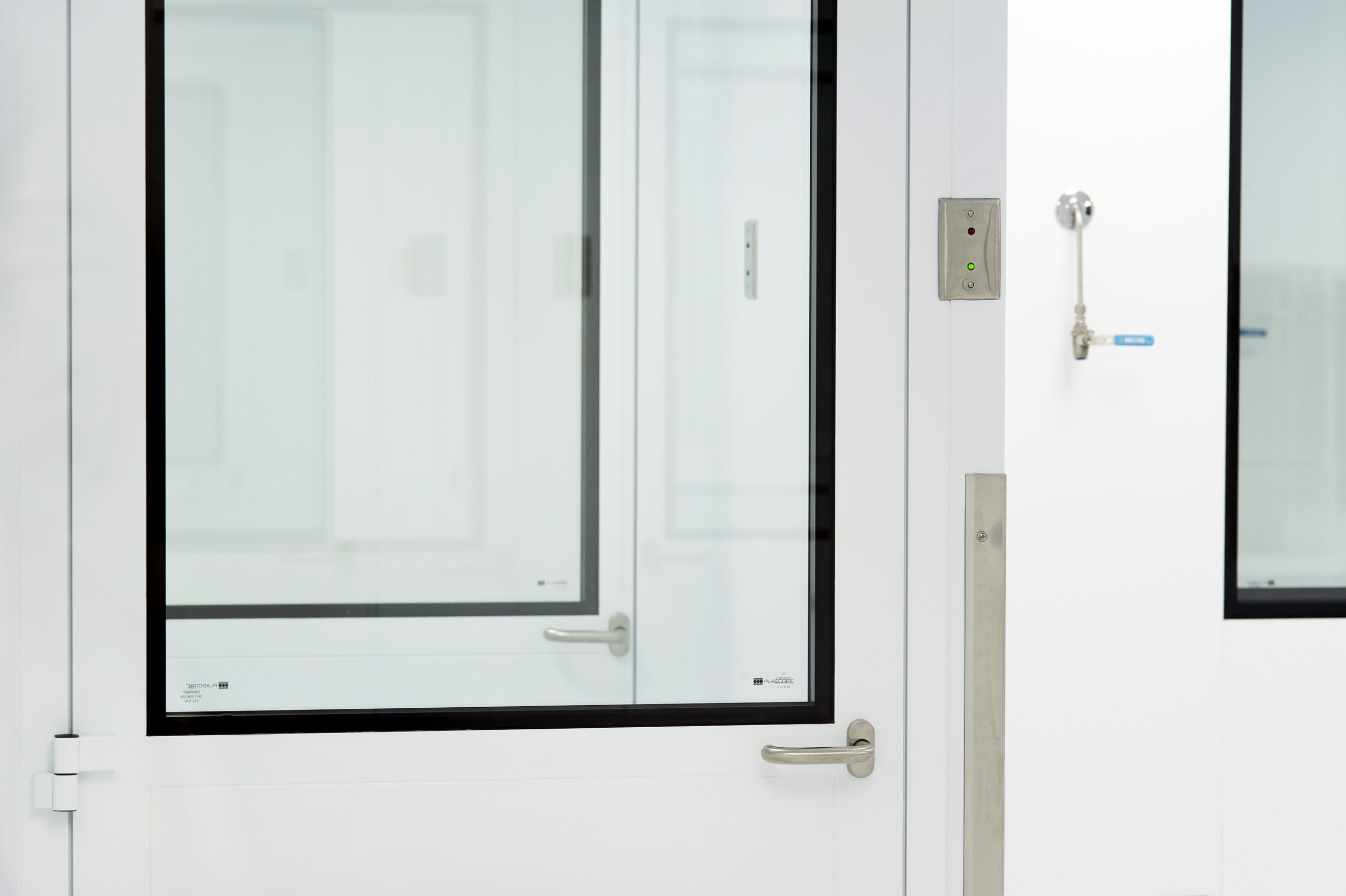
Pharmaceutical Cleanroom Fundamentals
Pharmaceutical cleanrooms serve as the backbone of drug manufacturing operations. They provide the controlled environment necessary for producing pharmaceutical products that meet stringent quality and safety standards. Reliable pharma cleanroom spaces maintain extremely low levels of airborne particles while controlling other environmental factors like temperature and humidity:
Structural Elements of Pharmaceutical Cleanroom Design
The design of pharmaceutical cleanrooms typically incorporates several structural elements to maintain the required level of cleanliness. The architectural components include specialized wall systems, ceilings, flooring, and doors that prevent particle buildup and allow for thorough cleaning. These materials must be non-shedding, resistant to cleaning agents, and free from crevices where contaminants might accumulate.
Pharmaceutical cleanroom flooring deserves special attention, as it needs to be seamless, easy to clean, and able to withstand heavy equipment and chemical exposure. Wall systems typically feature smooth, non-porous surfaces with rounded corners to eliminate areas where particles might collect.
Air quality handling systems form the heart of pharmaceutical cleanroom operations. These systems control airflow patterns, maintain proper room pressurization, and filter incoming air to remove contaminants. Strategically positioned supply and return vents create airflow patterns that sweep particles away from critical process areas.
Classification Standards for Pharmaceutical Cleanrooms
Pharmaceutical cleanrooms are classified according to the maximum allowable concentration of airborne particles per cubic meter. The International Organization for Standardization (ISO) classification system provides a framework that pharmaceutical manufacturers must adhere to based on their specific processes:
- ISO Class 5 (Class 100): Required for the most critical operations such as sterile filling, where sterile medicinal products are directly exposed to the environment.
- ISO Class 6 (Class 1,000): Often used for supporting areas around critical zones and some aseptic processing applications.
- ISO Class 7 (Class 10,000): Commonly implemented for less critical pharmaceutical operations such as secondary packaging and quality control testing.
- ISO Class 8 (Class 100,000): Suitable for warehouse areas and other support spaces where product exposure is minimal.
Proper classification of cleanrooms in the pharmaceutical industry determines the maximum allowable particle concentration for specific manufacturing processes.
Air Management and Filtration Systems
The backbone of pharmaceutical cleanroom performance is the air filtration system. HEPA filters remove at least 99.97% of particles 0.3 microns and larger, while Ultra-Low Particulate Air (ULPA) filters capture even smaller contaminants.
Air quality change rates in pharmaceutical environments are substantially higher than in conventional spaces. These high air change rates help dilute and remove any particles generated during manufacturing processes. The air handling system also maintains a pressure cascade, with higher pressure in cleaner areas to prevent contamination from flowing into more critical spaces.
The layout of airflow systems is designed to move air from clean areas to less clean areas, following the principle of unidirectional flow. This approach helps sweep particles away from critical process zones and toward return vents.
Let Precision Environments handle your cleanroom design and engineering
needs with proven results that exceed ISO standards
Facing contamination control challenges?
Engineering Systems for Pharmaceutical Environments
The operational requirements of pharmaceutical cleanrooms demand specialized equipment and monitoring systems. These technologies work together to maintain environmental specifications and provide documentation for compliance:
Specialized Equipment and Control Technologies
Pharmaceutical cleanrooms require sophisticated equipment beyond standard building systems to maintain their controlled environments. These specialized systems work together to create and maintain the proper environmental conditions:
- Airlocks and Pass-Throughs: Create transitions between areas of different classifications while maintaining pressure differentials to prevent cross-contamination.
- HVAC Systems: Provide precise temperature and humidity control with specialized filtration components designed specifically for pharmaceutical environments.
- Pressurization Controls: Monitor and adjust room pressures continuously to maintain the pressure cascade from cleanest to less clean areas.
- Modular Wall Systems: Feature non-porous, non-shedding surfaces that can withstand repeated cleaning with harsh disinfectants.
- Specialized Lighting: Recessed and sealed fixtures that minimize particle accumulation and simplify cleaning procedures.
Each of these systems must be carefully integrated into the overall cleanroom design to ensure proper performance and regulatory compliance.
Environmental Monitoring Approaches
Environmental monitoring in pharmaceutical cleanrooms provides continuous verification of environmental conditions and early detection of potential issues. The monitoring program typically includes several complementary approaches:
- Particle Monitoring: Real-time and periodic sampling of airborne particle counts to verify compliance with the designated ISO classification.
- Microbial Monitoring: Regular testing of air, surfaces, and personnel to detect and quantify viable microorganisms in the controlled environment.
- Environmental Parameters: Continuous monitoring of temperature, humidity, pressure differentials, and air quality changes per hour to ensure consistency.
- Data Management Systems: Software platforms that collect, analyze, and report monitoring data while providing alerts for out-of-specification conditions.
- Trend Analysis: Regular review of monitoring data to identify patterns that might indicate developing problems before they become critical issues.
Comprehensive monitoring programs provide both real-time operational control and the documentation necessary to demonstrate ongoing compliance with regulatory requirements.
Personnel Systems and Contamination Prevention
Personnel represent the largest source of microbial contamination in pharmaceutical cleanrooms. Appropriate gowning procedures and garments help minimize this risk. Gowning materials must be non-shedding and capable of containing particles generated by the human body.
The level of gowning depends on the room classification. In ISO 5 environments, personnel typically wear full coveralls, hoods, face masks, goggles, boots, and multiple layers of gloves. Less stringent environments might require only lab coats, hair covers, and gloves.
Personnel training on proper gowning techniques, movement within the pharmaceutical cleanroom, and material handling procedures is essential. Even a well-designed cleanroom cannot compensate for poor operational practices.
Performance Maintenance and Operations
Maintaining cleanroom performance requires structured approaches to operations and cleaning. These pharmaceutical cleanroom maintenance procedures ensure consistent performance and compliance:
Operational Protocols for Pharmaceutical Environments
Standardized procedures govern all activities within pharmaceutical cleanrooms. These procedures cover equipment operation, material transfer, personnel movement, and cleaning activities. They provide step-by-step instructions that, when followed correctly, minimize contamination risks.
Documentation requirements for pharmaceutical cleanrooms are extensive. All cleaning activities, environmental monitoring results, maintenance operations, and operator training must be recorded and retained. This documentation demonstrates ongoing compliance with established standards.
Regular certification and requalification verify continued compliance with design specifications. These activities typically include airflow visualization studies, particle counting, filter integrity testing, and recovery time testing.
Sanitization and Maintenance Best Practices
Pharmaceutical cleanroom sanitization follows validated protocols designed to maintain the controlled environment without introducing contaminants. Proper cleaning techniques are helpful for preventing microbial growth and maintain particle control:
- Cleaning Agent Selection: Specialized non-residue forming disinfectants and sanitizers that are effective against expected contaminants while compatible with cleanroom surfaces.
- Directional Cleaning Method: Techniques that progress from cleanest to less clean areas and from ceiling to floor to prevent cross-contamination during the cleaning process.
- Specialized Equipment: Dedicated tools like flat mops with disposable covers, autoclavable buckets, and filtered vacuums designed specifically for pharmaceutical cleanroom applications.
- Rotation Protocols: Scheduled alternation between different sanitizing agents to prevent the development of resistant microbial strains.
- Validation Testing: Post-cleaning verification through visual inspection, ATP testing, and microbiological sampling to confirm cleaning effectiveness.
These sanitization practices ensure the cleanroom maintains its specified classification between certification cycles while supporting continuous pharmaceutical manufacturing operations.
Precision Environments: Pharmaceutical Cleanroom Specialists
Since 1989, Precision Environments has specialized in designing and building high-performance controlled environments for the pharmaceutical industry and beyond. Our turnkey approach covers the entire implementation process from initial concept to certification and ongoing maintenance.
With expertise in ISO-compliant cleanrooms ranging from Class 3 to Class 8, we deliver customized solutions that integrate with your overall facility design while meeting all regulatory requirements. Our team of specialists partners with you to understand your specific processes and business goals, creating pharmaceutical cleanrooms that enhance your manufacturing capabilities while ensuring compliance with cGMP and other industry standards.
Ready to discuss your pharmaceutical cleanroom project? Contact our team to schedule a consultation.
Let Precision Environments handle your cleanroom design and engineering
needs with proven results that exceed ISO standards
Facing contamination control challenges?
Frequently Asked Questions
What are the requirements for a cleanroom?
Cleanroom requirements depend on the specific ISO classification needed for your manufacturing process, ranging from ISO 3 to ISO 8. The requirements include controlled levels of airborne particles, appropriate air handling systems with HEPA filtration, specified air changes per hour, temperature and humidity control, room pressurization, specialized wall and ceiling systems, and proper flooring designed for cleanroom applications.
Do cleanrooms need to be certified?
Yes, pharmaceutical cleanrooms must be certified to verify they meet the required ISO classification standards and good manufacturing practice guidelines. Certification involves comprehensive testing of air particle counts, air flow patterns, filter integrity, room recovery time, and pressure differentials by an accredited third-party agency that provides documentation proving the cleanroom meets all applicable standards.
How are cleanrooms cleaned?
Cleanrooms are cleaned using validated protocols with specialized cleaning agents, equipment, and techniques designed specifically for controlled environments. The cleaning process typically follows a top-to-bottom approach using non-shedding materials, with different procedures for walls, ceilings, equipment, and floors, along with documentation of all cleaning activities to maintain the validated state of the cleanroom.