Modular Aerospace Cleanrooms: Essential Solutions for Precision Manufacturing
In the aerospace and defense industries, precision is not just preferred — it’s paramount. When manufacturing components for aircraft, satellites, or spacecraft, even microscopic contaminants can lead to catastrophic failures with potentially life-threatening consequences. This is where modular aerospace and defense industry cleanrooms become essential, creating meticulously controlled environments that ensure the highest levels of cleanliness throughout the manufacturing process. As aerospace technology continues to advance, the need for specialized manufacturing environments grows increasingly critical, driving demand for custom-engineered modular cleanroom solutions that meet the industry’s exacting standards while offering adaptability for evolving requirements.
Let Precision Environments handle your cleanroom design and engineering
needs with proven results that exceed ISO standards
Facing contamination control challenges?
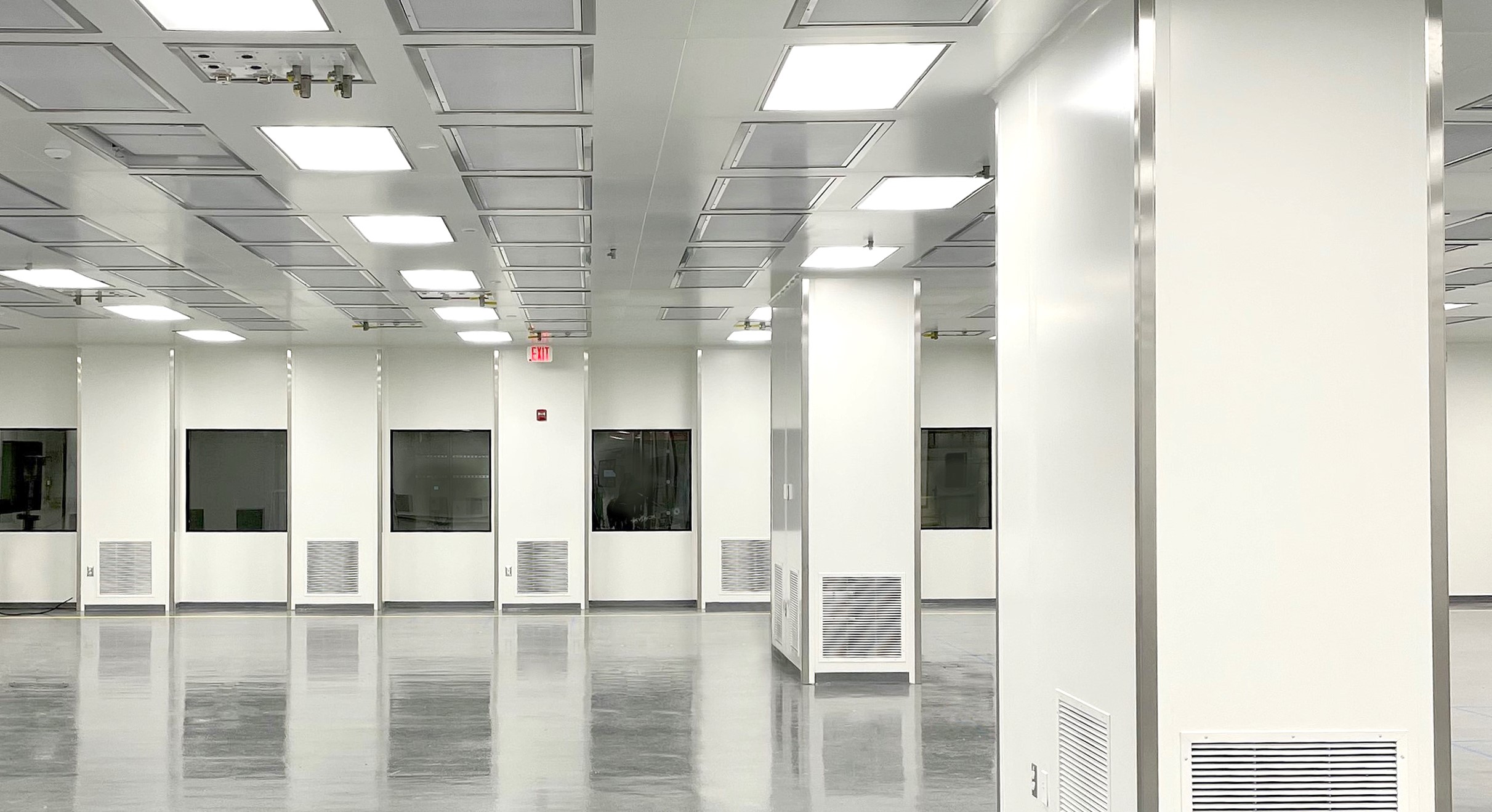
Modular Cleanroom Systems for Aerospace Applications
Aerospace manufacturing often involves working with materials and assemblies that must perform flawlessly in extreme conditions, from the freezing vacuum of space to the intense heat of atmospheric reentry. Components must be manufactured with unprecedented precision, and even the smallest contamination during production can compromise integrity, performance, and safety.
Modular cleanroom systems address these challenges by providing controlled environments specifically engineered to control temperature and humidity, manage static electricity, and maintain precise pressure differentials — all critical factors in aerospace manufacturing. These systems are designed with aerospace-specific requirements in mind, from accommodating oversized components to integrating specialized equipment and maintaining compliance with industry-specific standards.
What Makes a Cleanroom?
At its core, a cleanroom is an environment that controls airborne particulates, temperature, humidity, air pressure, airflow patterns, static electricity, and lighting to create optimal conditions for sensitive manufacturing processes. Unlike conventional manufacturing spaces, cleanrooms are built to stringent specifications that limit the number of particles per cubic meter of air.
What distinguishes a true cleanroom from simply a “clean room” is the implementation of validated engineering controls and standardized operational protocols that together maintain a scientifically verifiable level of cleanliness. In aerospace applications, these environments must often achieve ISO Class 7 or cleaner, meaning no more than 352,000 particles sized 0.5 microns or larger per cubic meter of air.
Key Components of Aerospace Modular Cleanrooms
Filtration Systems
- HEPA (High-Efficiency Particulate Air) filters that capture at least 99.97% of particles 0.3 microns and larger
- ULPA (Ultra-Low Particulate Air) filters for applications requiring even higher levels of filtration
- Pre-filtration systems that extend the life of more expensive terminal filters
- Fan filter units (FFUs) that distribute filtered air uniformly throughout the cleanroom
These filtration systems work together to create a cascading air purification process that continuously removes particles from the environment, ensuring the air remains within specified cleanliness classifications.
Structural Elements
- Modular wall panels with non-shedding, cleanroom-compatible surfaces
- Ceiling grid systems designed to accommodate filtration units and lighting
- Flooring systems that minimize particulate generation and facilitate cleaning
- Airlocks and gowning rooms that serve as transitional spaces between the outside environment and the cleanroom interior
The modular nature of these structural components allows for precise configuration to meet specific aerospace manufacturing requirements while accommodating future modifications as needs evolve.
Environmental Control Systems
- Dedicated HVAC systems calibrated to maintain precise temperature and humidity levels
- Monitoring equipment that continuously verifies environmental parameters
- Control systems that automatically adjust air handling units to maintain setpoints
- Alarm systems that alert operators to any deviations from specified parameters
These systems work in concert to create a stable manufacturing environment where aerospace components can be produced with minimal risk of environmental factors affecting quality or performance.
ISO Classifications and Industry Standards
Aerospace and defense cleanrooms typically adhere to ISO 14644-1 standards, which define cleanroom classifications based on the maximum allowed concentration of airborne particles. For aerospace applications, cleanrooms generally fall within ISO Class 5-8, with the specific classification determined by the sensitivity of the components being manufactured.
Beyond ISO standards, aerospace cleanrooms often must comply with additional industry-specific requirements such as AS9100 quality management systems, NASA standards for space flight hardware, or ASTM E2352 for aerospace manufacturing. These standards address particulate control and factors such as electrostatic discharge protection, outgassing prevention, and microbial control that are particularly relevant to aerospace applications.
Compliance with these standards isn’t merely a regulatory checkbox — it’s a fundamental requirement for ensuring that manufactured components will perform reliably under the extreme conditions encountered in aerospace applications.
Let Precision Environments handle your cleanroom design and engineering
needs with proven results that exceed ISO standards
Facing contamination control challenges?
Benefits of Modular Cleanrooms in Aerospace Manufacturing
Cost-Effectiveness and Scalability
Compared to traditional cleanroom construction, modular cleanrooms offer significant cost advantages throughout their lifecycle. The prefabricated nature of modular systems reduces initial construction costs by minimizing on-site labor and shortening the construction timeline. This approach also reduces waste, as components are precision-manufactured to exact specifications in a controlled factory environment.
Modular cleanrooms also facilitate scalability, allowing aerospace manufacturers to start with a configuration that meets current needs while enabling easy expansion as production requirements grow.
This scalability extends to classification levels as well — a modular cleanroom initially built to ISO Class 7 specifications can often be upgraded to ISO Class 6 or even Class 5 through modifications to filtration systems and operational protocols, without the need for complete reconstruction.
Quick Installation and Minimal Disruption
For aerospace manufacturers, production delays can have cascading effects on project timelines and costs. Modular cleanroom systems significantly reduce installation time compared to conventional construction, with many systems operational within weeks rather than months. This accelerated timeline minimizes disruption to existing operations and allows new manufacturing capabilities to come online faster.
The installation process itself is also less disruptive, as the majority of components arrive pre-fabricated and ready for assembly. This eliminates many of the dust-generating construction activities associated with traditional builds, which is particularly important when installing a cleanroom within an existing manufacturing facility where ongoing operations must continue uninterrupted.
Flexibility and Future Adaptability
Perhaps the most significant advantage of modular cleanrooms for aerospace applications is their inherent adaptability. As manufacturing processes evolve or new programs commence, modular systems can be reconfigured, expanded, or even relocated to accommodate changing requirements. This flexibility is invaluable in the aerospace industry, where contract requirements and production volumes can shift significantly over time.
Modular systems also offer adaptability for technology integration. As new monitoring systems, automation capabilities, or process equipment becomes available, modular cleanrooms can be more easily modified to incorporate these advances without the extensive retrofitting often required in conventionally constructed environments.
Critical Design Features for Aerospace Applications
Advanced Air Filtration and Pressure Control
Aerospace manufacturing frequently involves materials and processes that generate particulates or fumes that must be carefully controlled. Advanced filtration systems in aerospace cleanrooms not only remove ambient particles but also capture process-generated contaminants through strategically designed air return pathways and specialized extractors.
Pressure cascades represent another critical design feature, creating a hierarchy of pressurization that ensures airflow always moves from more critical to less critical areas. This prevents cross-contamination between different manufacturing zones and provides an additional barrier against the infiltration of external contaminants.
Material Selection and Surface Requirements
The materials used in aerospace cleanroom construction must satisfy multiple demanding criteria. Surfaces must be non-shedding, resistant to cleaning agents, electrostatically dissipative where required, and free from materials that could outgas volatile compounds that might contaminate sensitive components.
For aerospace applications, materials must also avoid containing silicones, which can volatilize and deposit on optical surfaces or electronic components with devastating effects on performance. This restriction extends beyond the cleanroom structure itself to include seals, gaskets, and even some types of lubricants used in equipment.
Environmental Control Systems
Beyond particulate control, aerospace manufacturing often requires precise management of temperature, humidity, and sometimes gas composition within the cleanroom environment. Control systems must maintain these parameters within narrowly defined tolerances while adapting to variables such as heat loads from equipment, personnel presence, and external environmental fluctuations.
These environmental control systems incorporate redundancy and fail-safe features to ensure the continuity of critical parameters, even during maintenance activities or in the event of primary system failures. This level of reliability is essential when manufacturing components that might be inaccessible for repair once deployed in aircraft or spacecraft.
Partnering with Experts for Your Aerospace Cleanroom Needs
Implementing modular aerospace cleanrooms becomes a seamless process when you partner with experienced specialists who understand your unique challenges. With Precision Environments, you’ll benefit from working with a team that brings over 30 years of experience designing turnkey controlled environments specifically engineered for aerospace manufacturing’s demanding requirements.
Your manufacturing processes, regulatory requirements, and operational goals will form the foundation of a cleanroom solution that precisely aligns with your needs. From initial concept through certification and ongoing maintenance, you’ll receive expert guidance and implementation support that creates high-performing environments, enhancing your aerospace manufacturing capabilities and ensuring the integrity of your critical components. Like a mission control center supporting a successful launch, your specialized cleanroom environment will provide the foundation for manufacturing excellence that drives your business forward.
Request a consultation to discuss how our custom-engineered cleanroom solutions can support your aerospace manufacturing objectives.
Let Precision Environments handle your cleanroom design and engineering
needs with proven results that exceed ISO standards
Facing contamination control challenges?
FAQ
How do modular cleanrooms differ from traditional cleanroom construction?
Modular cleanrooms utilize prefabricated components that can be assembled on-site, offering faster installation, greater flexibility for future modifications, and potential cost savings compared to traditional construction.
What ISO classification is typically required for aerospace manufacturing?
Aerospace manufacturing typically requires cleanrooms ranging from ISO Class 5 (100) to ISO Class 8 (100,000), with ISO Class 7 (10,000) being the most common classification for general aerospace component manufacturing. The specific classification needed depends on the sensitivity of the components being produced, with fine electronics and optical devices often requiring more stringent standards than structural elements.
Can modular aerospace cleanrooms be relocated if production needs change?
Yes, one of the key advantages of modular cleanrooms is their ability to be disassembled, relocated, and reassembled with minimal waste. Conventional construction typically requires complete demolition and rebuilding, while modular systems can be moved to new locations and reconfigured to meet changing production requirements, protecting your initial investment and providing operational flexibility.
How long does it typically take to install a modular aerospace cleanroom?
Installation timelines for modular aerospace cleanrooms typically range from 6 to 12 weeks depending on size, complexity, and classification requirements. The accelerated timeline minimizes production disruptions and allows new manufacturing capabilities to come online faster.