ISO 7 Cleanroom Classifications: Balancing Cleanliness with Operational Efficiency
ISO 7 cleanrooms balance effective contamination control with practical operating conditions for many manufacturing scenarios. Manufacturing in controlled environments benefits from reduced particle levels while avoiding higher classifications’ extreme restrictions and costs. Creating a successful ISO 7 space requires experienced design expertise that addresses classification requirements without unnecessary complexity, resulting in cleanrooms that protect products while supporting daily production activities.
Access the cleanroom knowledge base for detailed technical specifications on ISO classifications, airflow designs, and material requirements.
Let Precision Environments handle your cleanroom design and engineering
needs with proven results that exceed ISO standards
Facing contamination control challenges?
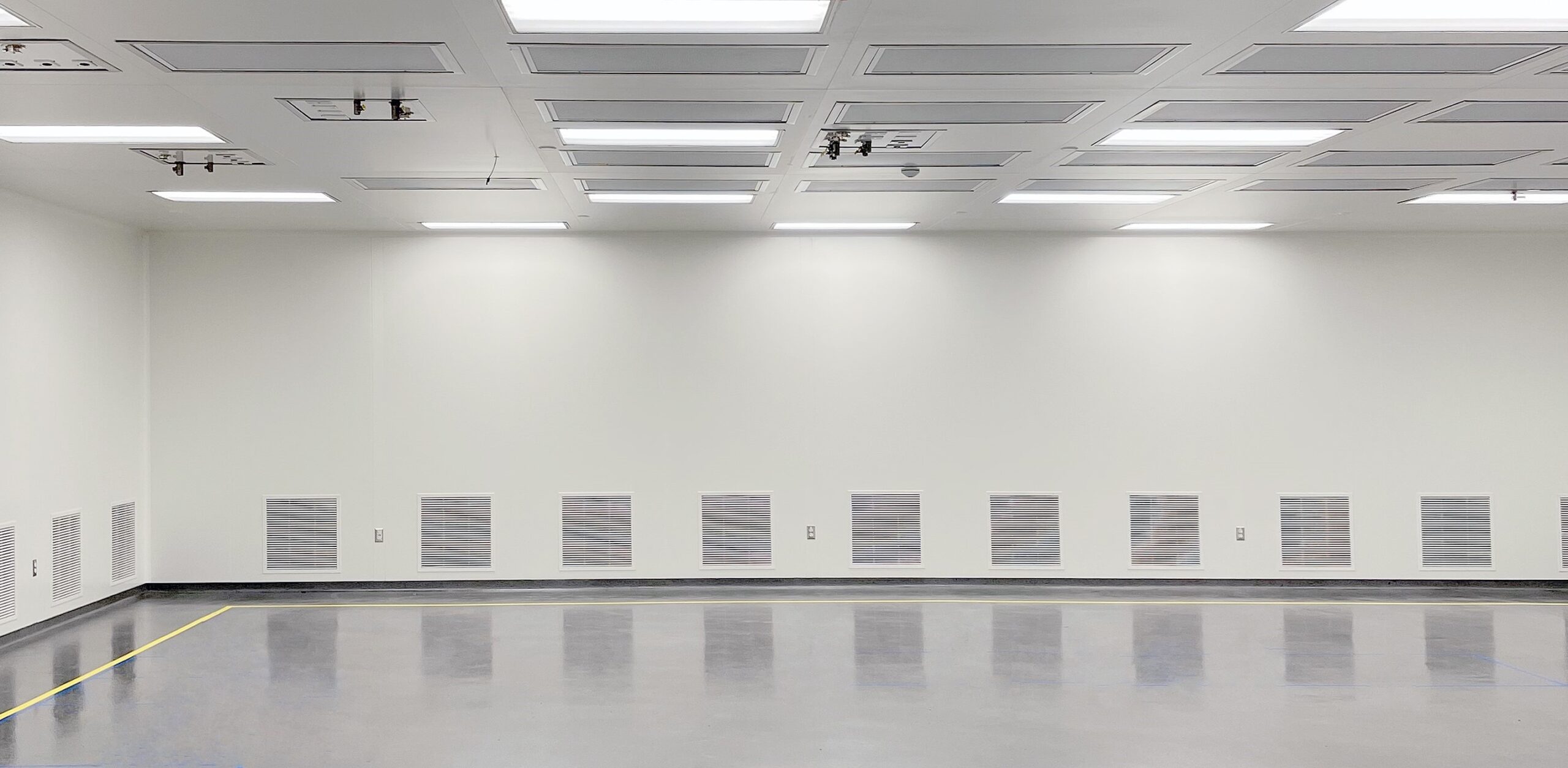
Manufacturing in Controlled Environments
The cleanroom classification system sets measurable standards for particulate control that directly impact manufacturing quality and consistency. Internationally recognized specifications provide clear design targets for engineers and verification benchmarks for certification:
ISO 7 Cleanroom Purpose and Applications
ISO 7 excels for pharmaceutical cleanrooms, precision industrial assembly, and medical device cleanrooms, where controlling airborne contamination directly affects product quality. ISO 7 spaces provide the right level of protection for injectable medications, implantable devices, and sensitive electronics through engineered cleanroom filtration and HVAC systems. Manufacturing teams avoid the substantial cost increases of higher classifications required for semiconductor fabrication or cell therapy production while still maintaining product protection.
Global Standards for Cleanroom Design
The ISO 14644-1 standard provides a clear, measurement-based system for categorizing cleanroom environments according to their air cleanliness levels. This internationally recognized approach defines specific particle concentration limits that shape the design and verification of controlled environments across industries:
- ISO Cleanroom Classification Scale: Ranges from ISO 1 (cleanest) to ISO 9 (least restrictive), with each level having precisely defined maximum particle concentrations.
- Measurement Standards: Based on particles per cubic meter of air, providing more precise measurements than the older Federal Standard 209E system.
- Particle Size Requirements: Each ISO class specifies allowable concentrations for multiple particle sizes, with the 0.5μm measurement typically serving as the primary reference point.
- Industry References: While ISO standards are officially recognized, many specifications still reference both systems (e.g., “ISO 7/Class 10,000”) for clarity across industry professionals.
Manufacturing processes requiring higher purity than ISO 7 benefit from ISO 6 cleanroom engineering expertise.
Where ISO 7 Stands in Cleanroom Classifications
ISO 7 environments (formerly “Class 10,000” under FS209E) allow a maximum of 352,000 particles (≥0.5 μm) per cubic meter. This represents substantially better contamination control than ISO 8 spaces while avoiding the higher costs associated with ISO 5 or ISO 6 requirements. For many industrial cleanrooms, ISO 7 hits the sweet spot of performance and practicality.
Let Precision Environments handle your cleanroom design and engineering
needs with proven results that exceed ISO standards
Facing contamination control challenges?
Technical Specifications for ISO 7 Cleanroom Design
Engineering ISO 7 and modular cleanrooms involves precise integration of multiple systems to maintain classification while supporting manufacturing operations:
Particle Count Requirements and Testing
ISO 7 environments must maintain specific particle limits:
- Primary Particle Limit: Maximum concentration of 352,000 particles (≥0.5 μm) per cubic meter establishes the baseline ISO 7 classification requirement.
- Secondary Particle Standard: Additional limit of 83,200 particles (≥1.0 μm) per cubic meter provides control of larger particulates.
- Verification Protocol: Regular particle count testing across multiple locations confirms the ISO 7 limits are consistently maintained throughout operations.
Temperature and Humidity Control Parameters
Beyond particle control, ISO 7 cleanrooms maintain precise environmental conditions. Temperature stability typically ranges within ±2°F, with relative humidity maintained within ±5% of setpoint. ISO 7 conditions remain stable regardless of external conditions or internal heat loads from equipment inside the cleanroom.
Air Delivery Systems and Change Rates
Proper air management forms the foundation of modular cleanroom design and performance:
- Air Exchange Rate: Typically 60-90 complete air changes per hour remove airborne particles and maintain classification levels.
- Filtration Systems: HEPA filtration of all supply air removes 99.97% of particles at 0.3 microns, providing clean air introduction.
- Pressure Differential Controls: Carefully engineered pressure cascades between adjacent spaces prevent migration of contaminants from less clean areas.
- Directional Airflow Design: Specific airflow patterns sweep particles away from critical manufacturing areas toward returns, enhancing contamination control.
Maintaining ISO 7 Cleanroom Performance
The long-term success of an ISO 7 cleanroom depends on specific operational protocols and maintenance:
Surface Selection and Cleaning Protocols
ISO 7 cleanrooms require specific surface materials and cleaning procedures:
- Cleanable Surface Materials: All interior finishes feature chemical-resistant, non-shedding properties that maintain integrity through thousands of cleaning cycles.
- Contamination-Resistant Design: Coved corners and minimal horizontal surfaces prevent particle accumulation and allow more effective cleaning processes.
- Validated Cleaning Methods: Maintenance protocols use only tested cleanroom-approved agents and techniques that remove contaminants without introducing new particles.
- Documentation Systems: Detailed cleaning schedules with sign-offs for all surface types provide verification of consistent maintenance standards.
Personnel Procedures and Training Requirements
People working inside ISO 7 and modular cleanroom environments follow specific protocols to minimize contamination potential during manufacturing operations. Personnel management includes multi-stage gowning procedures with specialized cleanroom garments designed to prevent particle shedding. Staff receive documented training on movement techniques and behaviors that reduce particulate generation during activities. Material transfer procedures through airlocks or pass-throughs maintain cleanroom integrity by preventing direct exposure to less-controlled adjacent spaces, preserving the controlled environment’s classification.
Certification and Performance Verification
Regular testing confirms continued compliance with ISO cleanroom classification standards:
- Particle Verification Testing: Regular sampling confirms airborne particle concentrations remain below ISO 7 limits across multiple locations throughout the space.
- Filter Performance Validation: HEPA filter integrity testing identifies any potential leakage or bypass that could compromise classification levels.
- Airflow Pattern Analysis: Smoke studies verify appropriate air movement patterns that sweep particles away from critical process areas.
- Compliance Documentation: Comprehensive testing reports provide verification of continued classification adherence for regulatory and quality assurance purposes.
Let Precision Environments handle your cleanroom design and engineering
needs with proven results that exceed ISO standards
Facing contamination control challenges?
Precision Environments: Your ISO 7 Cleanroom Partner
Since 1989, Precision Environments has designed and built ISO 7 cleanrooms for pharmaceutical, medical device, and industrial manufacturing facilities. Our complete project management covers initial concept through certification and ongoing maintenance, delivering classified spaces that maintain standards while fitting production requirements.
With over 1,000 cleanroom projects designed, built, and certified in nearly every state and across 15 countries, we know how to ensure cleanroom performance and manufacturing quality through intentional environmental control. Contact us today at (513) 847-1510 to discuss your ISO 7 cleanroom project.
Frequently Asked Questions
Is ISO class 7 or 8 better?
ISO class 7 provides about 10 times better contamination control than ISO class 8, making it suitable for more sensitive applications like injectable pharmaceuticals. The choice between classifications should be based on specific process requirements and regulatory standards, as higher classifications increase construction and operational costs.
How do I clean my ISO 7 cleanroom?
Cleaning an ISO 7 cleanroom requires specialized cleanroom-approved agents and non-shedding tools with documented procedures moving from the ceiling to the floor. The most reliable techniques include overlapping wiping patterns and progressing from cleanest to less clean areas to prevent recontamination.