Cleanroom HVAC Design: Engineered Systems for Optimal Performance
Cleanroom HVAC design requires precise engineering to establish the environmental parameters necessary for controlled environments. The HVAC system forms the backbone of any cleanroom design and directly impacts its classification, optimal conditions of performance, and compliance with industry standards.
Let Precision Environments handle your cleanroom design and engineering
needs with proven results that exceed ISO standards
Facing contamination control challenges?
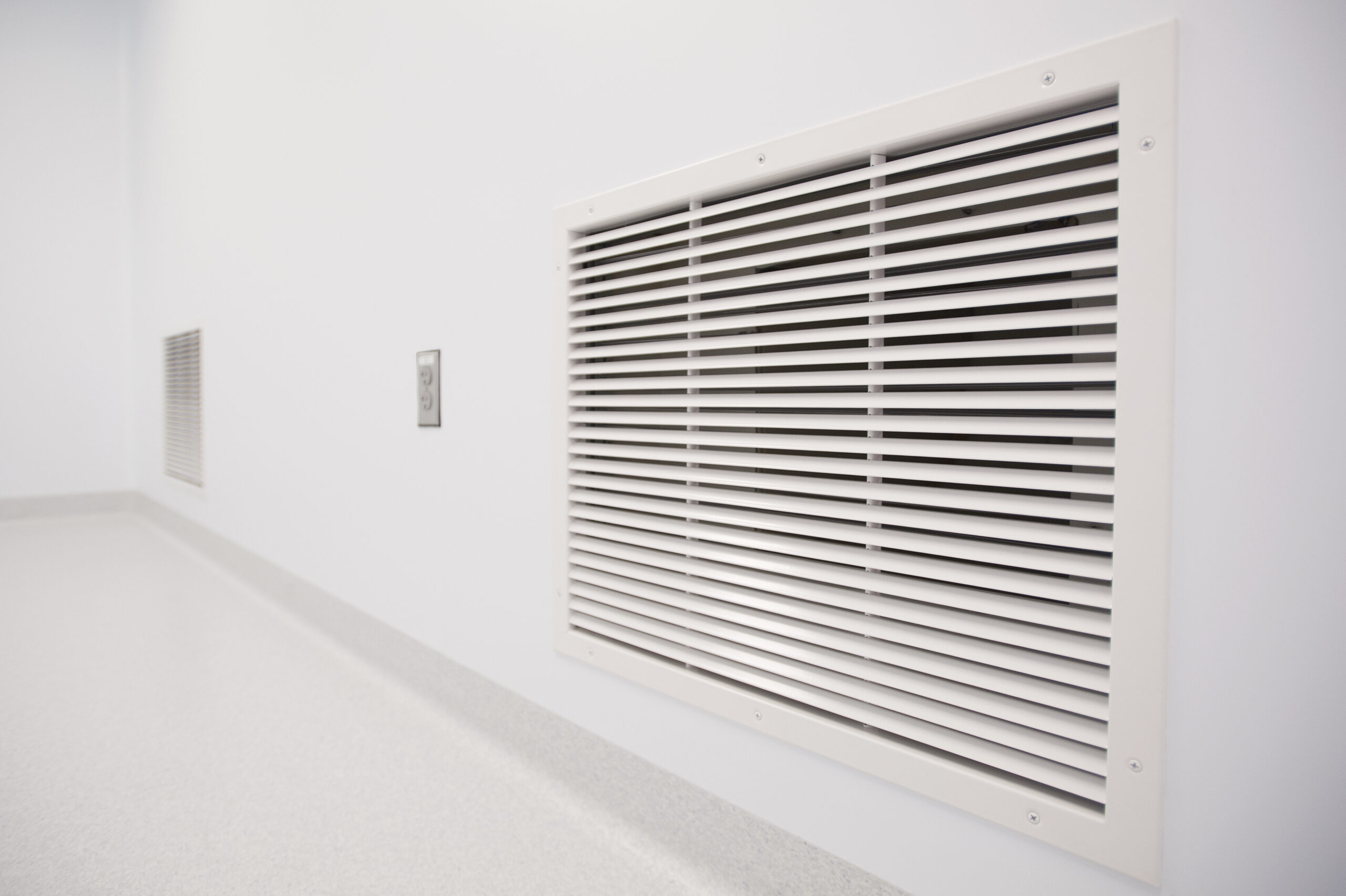
Cleanroom Design Considerations, Classifications, and HVAC Requirements
HVAC systems must meet precise air quality and environmental control specifications based on cleanroom use and classification. These requirements directly determine component selection, sizing, and design approach, establishing the foundation for optimal performance across pharmaceutical, semiconductor, and other critical manufacturing environments.
Upgrade your critical facilities with powerful cleanroom split DX HVAC systems designed for maximum performance in controlled environments.
Cleanroom Construction Management
Your project is critical and needs to be treated as such. Effective cleanroom construction management avoids delays, cost overruns, and substandard quality due to inefficient scheduling, poor oversight, and inadequate communication. Safety risks decrease when regulations and standards are followed, and mismanaged resources and project disruptions are mitigated through professional cleanroom construction management.
Cleanroom Concept & Planning
Every cleanroom concept and planning project has unique goals, objectives, and challenges. But meeting requirements, understanding processes, and identifying parameters aren’t enough. The most successful projects always start with a solid cleanroom plan that aligns with your unique business imperatives as well as regulatory, compliance, and classification requirements. Like physicians, the concept is to prepare a concept and planning strategy based on these specifications.
ISO Standards and Cleanroom Classifications
ISO 14644-1 establishes the standard cleanroom classifications from ISO Class 1 (most stringent) to ISO Class 9 (least stringent). These cleanroom classifications directly determine key HVAC design parameters that must be implemented to establish the required cleanliness level:
- ISO Class 3-4: Requires extremely high air change rates of 300-600 ACH and 100% HEPA filtration with unidirectional airflow patterns.
- ISO Class 5-6: Needs air change rates of 100-300 ACH with terminal HEPA filtration and typically employs a combination of laminar flow in critical areas.
- ISO Class 7-8: Requires 30-80 ACH with HEPA filtration covering 15-25% of ceiling area and can utilize non-unidirectional airflow design.
- ISO Class 9: Needs minimal 10-20 ACH with standard filtration and conventional HVAC design approaches.
Different rooms within a single facility can have different ISO ratings based on their specific functions, from ISO 8 down to ISO 5, and occasionally ISO 4 for specialized applications. Some controlled environments, like CNC manufacturing spaces, are controlled but not ISO certified and typically fall above ISO 8.
Meeting Regulatory Compliance Standards
Cleanroom HVAC systems must satisfy ISO 14644, FDA regulations, and cGMP requirements through proper documentation, validation protocols, and performance testing. Life sciences applications follow interpretable guidelines while meeting the required specifications.
Regulatory & Compliance Consulting
Critical environments ensure both manufacturing efficiency and regulatory compliance. Any company requiring a controlled environment inherently has a highly sensitive manufacturing process. Regulatory and compliance consulting programs like PRECEDE guide and guarantee that your modular cleanroom — from design and layout to equipment, materials, personnel, and material flow, is built to meet your industry’s exact specifications and regulatory standards, ensuring optimal performance and compliance.
Cleanroom Maintenance & Service
Everyone knows that preventive maintenance extends a vehicle’s life and enhances performance by addressing potential issues before they become major problems. Cleanroom maintenance and service operate the same way—regular upkeep is essential to ensure optimal functionality and longevity. Professional teams help you stay ahead of any issues with proactive maintenance services. When emergencies arise, rapid response services act quickly to ensure your cleanroom continues to perform at its best without costly downtime or disruptions.
Let Precision Environments handle your cleanroom design and engineering
needs with proven results that exceed ISO standards
Facing contamination control challenges?
Critical Air Parameters for Different Cleanroom Types
Different cleanroom types require specific air supply parameters based on their applications and industry requirements. Proper HVAC system design must account for these specialized parameters to create optimal production conditions:
- Pharmaceutical Manufacturing: Demands precise humidity control (30-65% RH) with minimal fluctuation.
- Semiconductor Production: Requires exceptional temperature stability (±0.5°F or better) to support nanometer-scale process accuracy.
- Medical Device Assembly: Necessitates elevated air flow change rates (40-100 ACH) combined with strategic airflow patterns.
- Biotechnology Applications: Calls for specialized pressure cascades and dedicated exhaust systems.
Key Components of Cleanroom HVAC Systems
The following integrated components establish controlled environments while determining overall system performance and reliability:
Air Handling Units and Distribution Systems
Air handling units (AHUs) manage the collection, conditioning, and distribution of air throughout the cleanroom. The air handler must be sized to accommodate the required air change rates while maintaining a consistent supply of air temperature and humidity. Distribution systems may include ductwork, terminal filter modules, plenums, Fan Filter Units (FFUs), or a combination depending on the cleanroom design.
High-Efficiency Particulate Air (HEPA) Filtration Systems
HEPA filters are fundamental to cleanroom HVAC design, capturing at least 99.97% of particles 0.3 microns or larger. The filtration strategy must be carefully engineered as part of the overall HVAC system to ensure consistent air quality throughout the controlled environment:
- HEPA Filtration: Standard H14 HEPA filters remove at least 99.97% of particles ≥0.3μm, creating the foundation for ISO 7-8 cleanroom environments.
- ULPA Filtration: Ultra-Low Particulate Air filters capture 99.9995% of particles ≥0.12μm, necessary for ISO 3-5 applications in semiconductor and nanotechnology sectors.
- Filter Housing Design: Incorporates gel-seal or knife-edge technologies to eliminate bypass leakage at filter perimeters while allowing for regular integrity testing.
- Filter Arrangement: Strategic placement in ceiling grids, terminal filters, fan filter units, or custom plenums determines airflow patterns throughout the space.
Temperature and Humidity Control Equipment
Precise control of temperature and humidity levels is necessary for process stability. Cooling coils, heating elements, and humidification/dehumidification systems must be sized to handle both normal loads and peak loads during production. Controlled environments often require ±1°F temperature stability and ±5% relative humidity stability.
Advanced Design Considerations for Cleanroom HVAC
These advanced design elements optimize airflow dynamics, energy efficiency, and control systems for maximum operational effectiveness:
Airflow Patterns and Room Pressurization Requirements
Airflow patterns in cleanrooms are designed to direct air movement in specific patterns while maintaining appropriate environmental conditions. Properly engineered airflow and room pressure relationships form the foundation of effective cleanroom performance:
- Unidirectional Flow: Creates a uniform 90 fpm laminar air curtain moving parallel to walls from ceiling to floor, ideal for ISO 5 and cleaner environments where product exposure occurs.
- Non-Unidirectional Flow: Utilizes controlled turbulent mixing at 20-60 air changes per hour in ISO 6-8 environments.
- Positive Pressurization: Maintains 0.03-0.05 inches water gauge differential between adjacent spaces to prevent infiltration of outside air into cleaner areas.
- Negative Pressurization: Creates an inward airflow of 0.05-0.10 inches water gauge in containment applications to protect surrounding areas.
Monitoring and Control Systems Integration
Automated systems with environmental sensors continuously monitor and adjust parameters to maintain specifications. Direct Digital Control (DDC) systems integrate operations, alarms, and compliance documentation while providing real-time alerts for any deviations.
Energy Efficiency and Cleanroom Sustainability Measures
Cleanroom HVAC systems typically consume substantial energy due to high air change rates and strict environmental controls required to maintain classification. Implementing these efficiency measures delivers both environmental and economic benefits throughout the cleanroom lifecycle:
- Heat Recovery Systems: Capture thermal energy from exhaust airstreams to pre-condition incoming makeup air, reducing energy usage by 30-50% in suitable applications.
- Variable Frequency Drives: Allow fan systems to modulate based on real-time demands, saving 15-40% of fan energy during non-peak operational periods.
- Low-Pressure-Drop Filtration: Incorporates mini-pleat HEPA designs and optimized housing configurations to reduce static pressure requirements while maintaining filtration efficiency.
- Demand-Based Controls: Implement occupancy-based or process-based reset strategies that adjust air change rates according to actual conditions.
Precision Environments: Masters of Cleanroom Engineering
For over 35 years, Precision Environments has defined industry excellence with 1,000+ specialized cleanroom installations across 15 countries. Our A2LA 17025 Accreditation guarantees uncompromising quality in every project. Our innovative modular systems evolve with your technology needs, ensuring your investment delivers long-term value.
Ready to dominate your market with superior manufacturing precision? Contact our engineering team today for a no-obligation consultation and discover how our proven cleanroom solutions can revolutionize your production environment.
Let Precision Environments handle your cleanroom design and engineering
needs with proven results that exceed ISO standards
Facing contamination control challenges?
Frequently Asked Questions
What ISO classification do I need for my pharmaceutical cleanroom?
Pharmaceutical cleanrooms typically require ISO 7-8 for general production and ISO 5-6 for critical processes like aseptic filling. Classification needs vary based on product requirements and regulations.
How do you calculate CFM for a cleanroom?
Calculate CFM by multiplying room volume by required air changes per hour (based on ISO classification) and dividing by 60. Consider classification requirements, heat load, and makeup air needs.