Understanding Cleanroom Design: Advanced Environments for Specialized Manufacturing
Cleanroom design is one of the most intricate fields in controlled environment engineering. A well-designed cleanroom provides the foundation for precision manufacturing processes required by industries such as pharmaceutical, semiconductor, biotech, and medical device production.
The design process must account for numerous factors, including particle count limitations, temperature stability, and proper airflow patterns. Sophisticated cleanroom HVAC design and humidity control systems work together to create these specialized environments. These precisely engineered spaces require expert design and construction to achieve classifications ranging from ISO Class 3 to Class 8, each serving specific manufacturing and research applications.
Let Precision Environments handle your cleanroom design and engineering
needs with proven results that exceed ISO standards
Facing contamination control challenges?
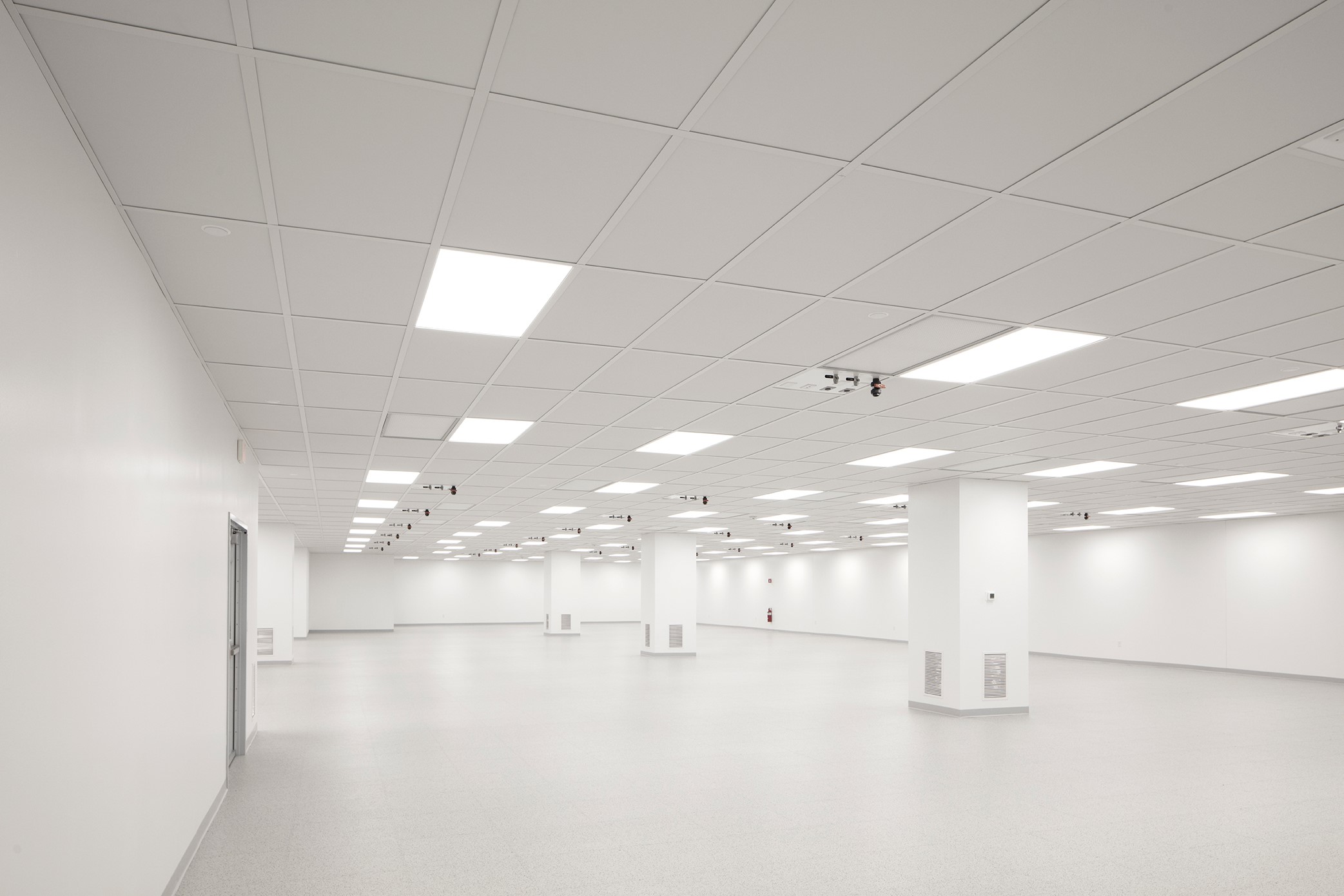
Cleanroom Classifications and Standards: The Foundation of Precision Design
The design of any cleanroom begins with understanding the required classification level. This determines virtually every aspect of the cleanroom construction, from filtration requirements to material selection. Quality cleanroom design services establish the framework for your manufacturing environment through intentional engineering and construction techniques that meet specific ISO standards:
ISO Standards and Classifications for Cleanroom Design
ISO 14644-1 establishes the primary classification system used in cleanroom design today. This standard defines cleanliness classes based on the maximum allowable concentration of particles per cubic meter. The classifications range from ISO Class 1 (most stringent) to ISO Class 9 (least stringent), with each level having specific requirements for cleanroom design implementation:
- ISO Class 3: Extremely stringent environment with maximum 1,000 particles (≥0.5μm) per cubic meter, typically used in semiconductor manufacturing.
- ISO Class 5: Permits maximum 3,520 particles (≥0.5μm) per cubic meter, common in aseptic pharmaceutical processing.
- ISO Class 6: Allows 35,200 particles (≥0.5μm) per cubic meter, suitable for less critical medical device manufacturing.
- ISO Class 7: Specifies 352,000 particles (≥0.5μm) per cubic meter, often used in pharmaceutical packaging.
- ISO Class 8: Designates 3,520,000 particles (≥0.5μm) per cubic meter, appropriate for general manufacturing cleanrooms.
Need a cleanroom designed to precise ISO specifications? Let Precision Environments handle your cleanroom design and engineering needs with proven results that exceed industry standards.
Key Design Principles: The Technical Foundation of Cleanroom Performance
Successful cleanroom design depends on precise engineering of several critical parameters. Particle concentration limits define the classification, but achieving and maintaining these specifications requires proper air changes per hour (typically 10-600 depending on classification), differential pressure control (usually +0.05″ to +0.08″ water column between adjacent spaces), and appropriate temperature and humidity control (often ±1°F and ±5% RH).
These parameters inform everything from HVAC sizing to wall system selection. Cleanroom flooring, ceiling systems, and material choices all work together to create the specialized environment your manufacturing processes require. Like a custom home builder focuses on structural integrity, we focus on these technical elements to deliver a cleanroom that performs to specification.
Federal Standard 209E Legacy in North America
Though officially replaced by ISO standards, Federal Standard 209E terminology still appears in some cleanroom design specifications in North America. This system classified cleanrooms by the number of particles per cubic foot, creating a different but related classification approach. Understanding the correlation between these legacy standards and current ISO classifications is essential for cleanroom design projects:
- Class 1: Equivalent to approximately ISO Class 3, allowing 1 particle (≥0.5μm) per cubic foot.
- Class 10: Roughly corresponds to ISO Class 4, permitting 10 particles (≥0.5μm) per cubic foot.
- Class 100: Comparable to ISO Class 5, with 100 particles (≥0.5μm) per cubic foot limit.
- Class 1,000: Similar to ISO Class 6, allowing 1,000 particles (≥0.5μm) per cubic foot.
- Class 10,000: Equivalent to ISO Class 7, with 10,000 particles (≥0.5μm) per cubic foot maximum.
- Class 100,000: Corresponds to ISO Class 8, permitting 100,000 particles (≥0.5μm) per cubic foot.
Core Elements of Advanced Cleanroom Design
The physical construction of a cleanroom requires application-specific components engineered to achieve classification requirements while supporting your operational needs. These design elements work together to create a sealed, controlled environment with precise environmental parameters—similar to how a custom home’s components work together to create a comfortable living space:
Airflow Patterns and Air Handling Units: Engineering for Performance
Cleanroom design incorporates specific airflow patterns based on your application and classification requirements. Selecting the appropriate airflow strategy requires understanding the fundamental approaches used in modern cleanroom design:
- Unidirectional Flow: Creates parallel air streams moving at uniform velocity (typically 90 ft/min) to direct airflow away from critical processes, ideal for ISO Class 5 and cleaner environments.
- Non-Unidirectional Flow: Utilizes controlled turbulent mixing to dilute and remove particles, commonly applied in ISO Class 6-8 cleanrooms where cost efficiency is important.
- Mixed Flow Systems: Combines unidirectional flow over critical processes with non-unidirectional flow in surrounding areas, optimizing both performance and operational costs.
- Fan Filter Units: Self-contained HEPA filter modules with dedicated fans, providing flexibility in cleanroom layout and maintenance.
- Pressurized Plenums: Create uniform pressure distribution above the cleanroom ceiling to ensure consistent air delivery through terminal filters.
- Return Air Pathways: Strategically positioned low wall or floor returns that direct air away from critical processes.
Facing contamination control challenges?
Let Precision Environments handle your cleanroom design and engineering needs with proven results that exceed ISO standards
Filtration Systems: The Heart of Cleanroom Performance
High Efficiency Particulate Air (HEPA) and Ultra Low Penetration Air (ULPA) filters form the backbone of any cleanroom design. HEPA filters remove 99.97% of particles 0.3 micrometers and larger, while ULPA filters capture 99.9995% of particles 0.12 micrometers and larger. The air filtration system design must account for the required clean air delivery rate, filter placement, and testing methods.
For ISO Class 5 and cleaner environments, terminal HEPA filters are typically installed at the ceiling level with sufficient coverage to provide uniform air distribution. The air filtration system often incorporates pre-filters to extend the life of the more expensive HEPA/ULPA filters, creating a cost-effective and efficient system designed for long-term performance.
Cleanroom Construction Components: The Structural Framework
Wall systems, ceiling grids, and specialized flooring form the physical structure of a cleanroom. These elements must meet strict performance requirements while supporting the equipment and processes housed within the controlled environment. Much like a custom home requires specialized materials and construction techniques, the selection of appropriate cleanroom components is fundamental to achieving the required classification:
- Modular Wall Panels: Pre-engineered panels with non-shedding, non-outgassing surfaces that provide smooth, cleanable walls with minimal seams and crevices for optimal performance.
- Cleanroom Flooring: Surfaces ranging from epoxy coatings with coved bases to ESD-dissipative vinyl and raised access flooring systems that accommodate utilities while supporting classification requirements.
- Ceiling Systems: Walkable or non-walkable grid systems that support terminal HEPA filters, lighting fixtures, and sprinkler heads while maintaining an air-tight seal.
- Window Systems: Flush-mounted, double-glazed panels that eliminate ledges and provide visibility without compromising the cleanroom envelope.
- Door Systems: Doors with appropriate seals, interlocks, and automation features that maintain pressure differentials while allowing efficient personnel and material flow.
- Pass-Through Chambers: Dedicated transfer points with interlocking doors that allow materials to enter or exit the cleanroom without compromising environmental conditions.
The Design Process for High-Performance Controlled Environments
Creating a successful cleanroom requires a structured approach that incorporates your specific requirements, regulatory standards, and process specifications. Our design-build process ensures the resulting environment meets both your operational needs and compliance requirements:
Concept Development and Requirements Analysis
The initial phase of our cleanroom design process focuses on understanding your specific processes, equipment, and personnel flows. This collaborative stage includes identifying the required classification, process utilities, equipment layout, and adjacency requirements.
Our team considers future flexibility needs, expansion possibilities, and maintenance access—creating the foundation for a cleanroom concept that balances technical performance with operational practicality and cost efficiency. Like a custom home builder begins with understanding how you’ll use the space, we start by thoroughly analyzing how your cleanroom will support your manufacturing processes.
Engineering Design and Documentation
Once we’ve defined your concept, our detailed engineering begins for architectural, mechanical, electrical, plumbing, and control systems. This phase transforms conceptual requirements into precise technical specifications that guide construction. Our specialized expertise allows us to develop a cleanroom solution:
- Architectural Drawings: Detailed plans showing wall systems, ceiling layouts, door locations, and material finishes that comply with cleanroom standards and support your process flow requirements.
- Mechanical Systems Design: HVAC schematics, including air filtration systems and handling units, ductwork layouts, filter locations, and control dampers sized to achieve specified air change rates and temperature/humidity control.
- Electrical Distribution: Power layouts addressing requirements for equipment, lighting, monitoring systems, and emergency backup while minimizing penetrations in the cleanroom envelope.
- Process Utilities: Designs for compressed air, process gases, purified water, and systems that support your manufacturing processes while maintaining cleanroom integrity.
- Control Systems: Building automation designs for monitoring and controlling environmental parameters, including air pressure differentials, temperature, humidity, and particle counts.
- Computational Models: Airflow simulations that validate filter placement, identify potential dead zones, and optimize air distribution for optimal performance.
Validation and Certification Planning
The final phase of our design process includes developing testing and certification protocols. These procedures verify that your constructed environment meets all specified requirements including particle counts, air change rates, pressure differentials, temperature, and humidity control.
Our designs incorporate appropriate testing ports, monitoring locations, and access points to enable ongoing verification of environmental conditions. Proper certification planning ensures your cleanroom will not only meet initial requirements but continue to perform as specified throughout its operational life.
About Precision Environments: Your Turnkey Cleanroom Design Partner
Since 1989, our team has delivered over 1,000 controlled environments across 15 countries, establishing a reputation for excellence in cleanroom design and construction. We offer end-to-end solutions from concept through certification and maintenance. Our approach integrates regulatory knowledge, engineering expertise, and construction experience to create environments that achieve ISO Class 3 to Class 8 specifications while supporting your specific manufacturing requirements.
Our portfolio includes pharmaceutical cleanrooms, semiconductors, biotech, modular cleanrooms, and medical device applications. Each project incorporates custom engineering for temperature and humidity control, air filtration, pressurization, and process utilities. We collaborate closely with you to develop solutions that enhance your operational capabilities while meeting strict regulatory standards.
Contact us today to discuss your next cleanroom project. Our team will guide you through the entire design-build process, from initial concept to final certification.
Facing contamination control challenges?
Let Precision Environments handle your cleanroom design and engineering needs with proven results that exceed ISO standards

Frequently Asked Questions
What is cleanroom design?
Cleanroom design is a specialized engineering discipline focused on creating controlled environments that maintain specific levels of air purity, temperature, and humidity. The design incorporates advanced wall systems, ceiling grids, filtration technologies, and mechanical systems to achieve the required classification. Proper design balances technical performance with operational considerations through detailed engineering techniques that ensure your manufacturing processes have the environment they need.
How does Precision Environments approach cleanroom construction?
Our cleanroom construction begins with establishing detailed specifications based on your classification requirements and process needs. The construction involves installing modular wall systems, specialized flooring, ceiling systems for HEPA filtration, and mechanical systems for proper air changes and pressurization. Our qualified teams follow strict protocols during installation to ensure proper sealing, system performance, and prepare your environment for certification.